Lightweight robots for optimized processes
Discover the future of automation with our state-of-the-art components for lightweight robotics. Our innovative solutions offer maximum flexibility and precision to make your production processes more efficient and cost-effective. Whether grippers, sensors or end-of-arm tooling – we have the right components for your individual requirements. With our expertise, we help you to master the challenges of automation and increase your productivity.
Start a new era of lightweight robotics now and let our experts advise you – contact us today!
Your benefits:
- Simple integration tailored to the robot
- Maximum performance with maximum safety
- System landscape for the entire value chain
- IP protection class for adverse environmental conditions
- Energy efficiency in production and application
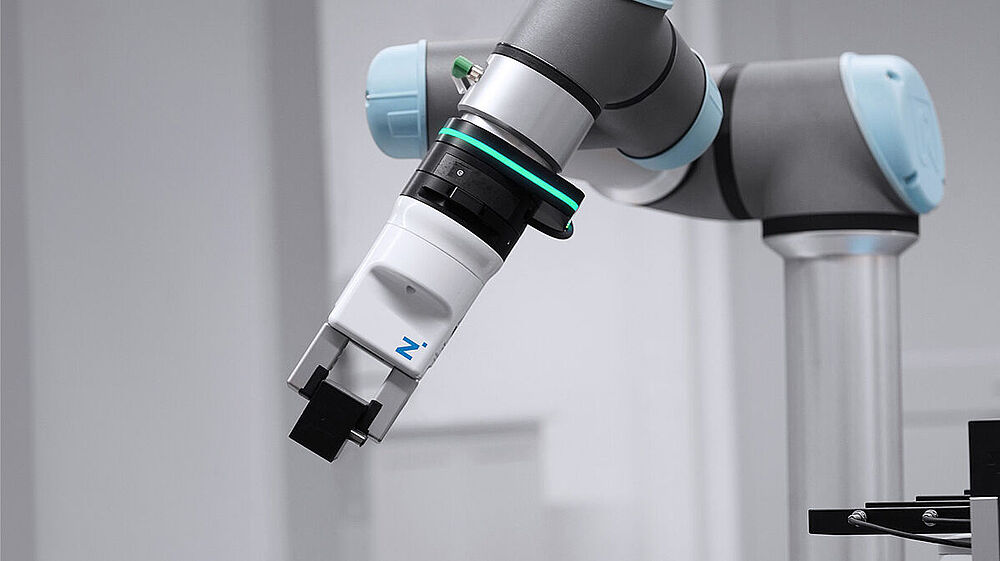
Why lightweight robots?
The ever-faster pace of technological development, the increasing number of different workpieces and, last but not least, the ever greater market penetration of robots have led to the trend towards lightweight robots. The simplified operation of these robots has opened up new industries and business areas. In terms of quick installation and commissioning, lightweight robots are also ideal for the target group of robot beginners. Both simple and relatively complex applications can be realized in combination with the right end effector.
HUMAN – ROBOT
DIFFERENT FORMS OF INTERACTION
Collaboration between humans and robots is associated with challenges in terms of safety precautions, but also with concerns on the part of employees. Here we provide an overview of various forms of interaction with (lightweight) robots. It is clear that the use of robotics holds enormous potential for companies in terms of efficiency, cost savings and reducing the workload of employees.
CONVENTIONAL COMPONENTS
Clearly demarcated work areas for robots are suitable for heavy work or work that is potentially dangerous for the employee. End effectors do not require any special HRC geometries or gripping force limitations, as employee contact is prevented by spatial limitations.
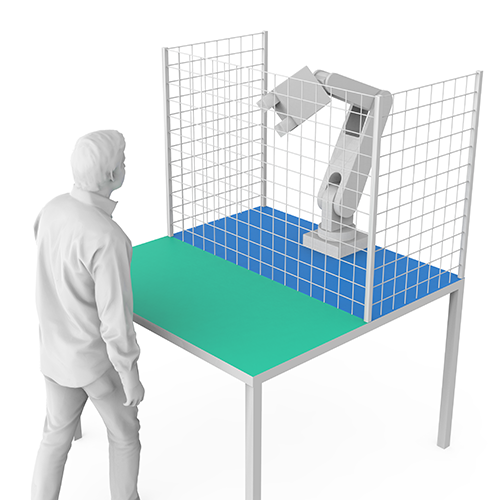
Automation cell
- Separated workspaces
- Workpiece holder in a secure area
- All gripper systems can be used
- Decoupled work
- No contact necessary
- Maximum speed
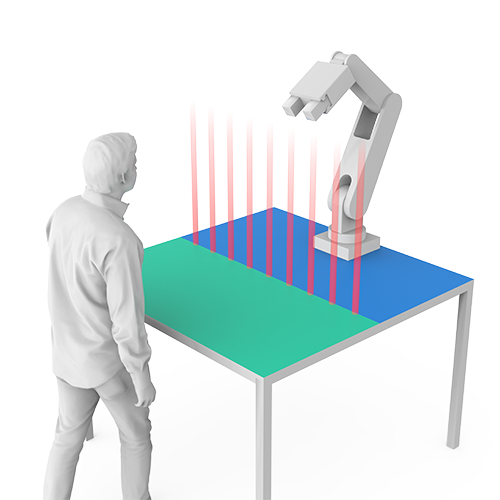
Coexistence
- Presence detection
- Workpiece holder in a secure area
- All gripper systems can be used
- Separated workspaces
- Decoupled work
- No contact necessary
- Reduced speed
HRC COMPONENTS
The advent of robotics in almost all areas of production worldwide and technical progress in the field of sensor and image processing technology have opened up the field of cooperating and collaborating robots to support humans (HRC) in the production process. This cooperation and collaboration gives people the freedom to open up new frontiers in work and to fill them in a way that is precise, flexible and efficient.
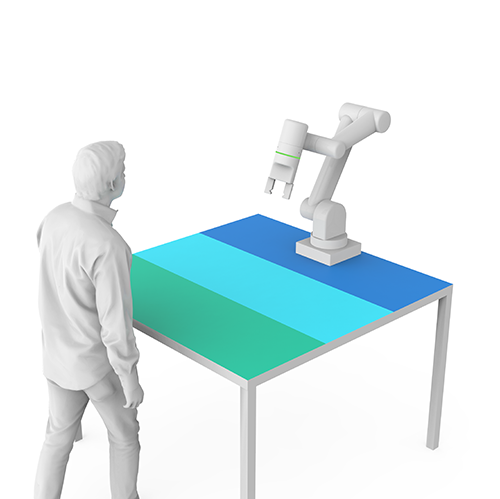
COOPERATION
- Zones of action
- Workpiece holder in the secured area
- Gripper with special HRC geometry
- Secure holding of the workpiece, even if the power supply fails
- Shared workspaces
- Coupled work
- No contact necessary
- Reduced speed
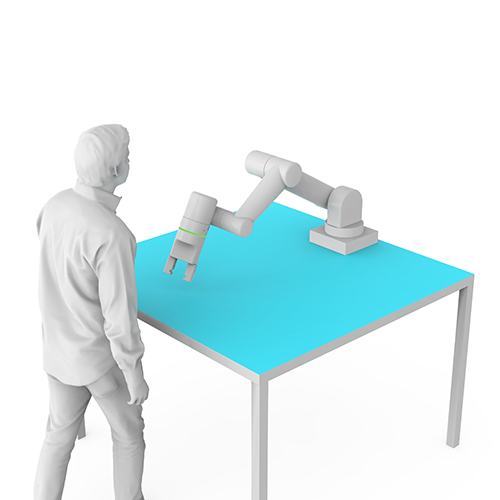
Collaboration
- Shared workspaces
- Workpiece holder in the unsecured area
- Gripper with special HRC geometry and safe gripping force control
- Gripping force limited to a max. of 140 N as per ISO / TS 15066
- Secure holding of the workpiece even if the power supply fails
- Coupled work
- Necessary amount of contact
- Reduced speed
Technology highlight: STANDARD INTERFACE
For robots and end effectors
MATCH End-of-Arm Ecosystem
Equipped with an extensive range of functions and universal communication interfaces, MATCH is compatible with all common lightweight robots on the market – an ideal system for cobots and conventional 6-axis robots.
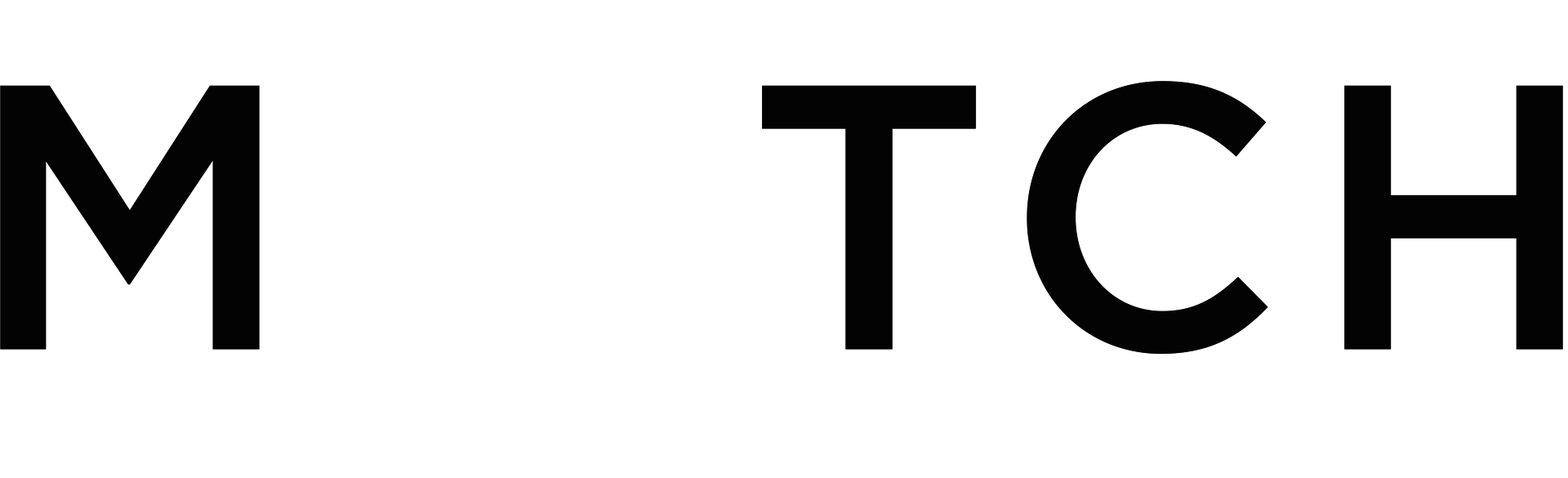
MATCH components can be recognized by this symbol.
Product of the Year 2023
The MATCH end-of-arm ecosystem is a milestone in robotics and has been named “Product of the Year 2023” by WEKA Business Medien GmbH https://www.zimmer-group.com/de/ueber-uns/news/produkt-news/newsdetails/match-als-produkt-des-jahres-ausgezeichnet In the “Handling, Assembly and Production Logistics” category, the Zimmer Group beat 11 competitors to take first place.
Applications as varied as the system – the application
Mobile and collaborative robotics or fully automated applications – just one flexible system gives the user access to a nearly unlimited range of uses from production and installation to warehouse logistics, shipping and even laboratory automation.

Standardization of the robot interface
One robot module – the entire range of compatible end effectors. Whether cobots, lightweight robots or conventional robots.

Easy installation – Plug & Work
Simplified machine communication thanks to the required communication parameters.

Flexible
Direct control and monitoring of robot functions using a software solution.

Complex robot applications
Can perform various tasks on a workpiece via automated end effector replacement.