Machines and plants
The mechanical engineering sector is under massive competitive pressure around the world. For 30 years now, we at Zimmer Group have been applying our technical expertise and many years of experience on behalf of our customers in the area of mechanical and plant engineering. We provide innovative developments and deliver the unique features that are required. We rely on a modular product system to offer you a tailor-made solution for your requirements. Let this page inspire you with some of our realized projects and application examples and take a look at our service portfolio!
Do you have questions or do you already have a specific project in mind for which you need support? Write to us!
Robot-based drilling technology
SYSTEM FOR AN OUTPUT OF UP TO 4 PARTS PER MIN
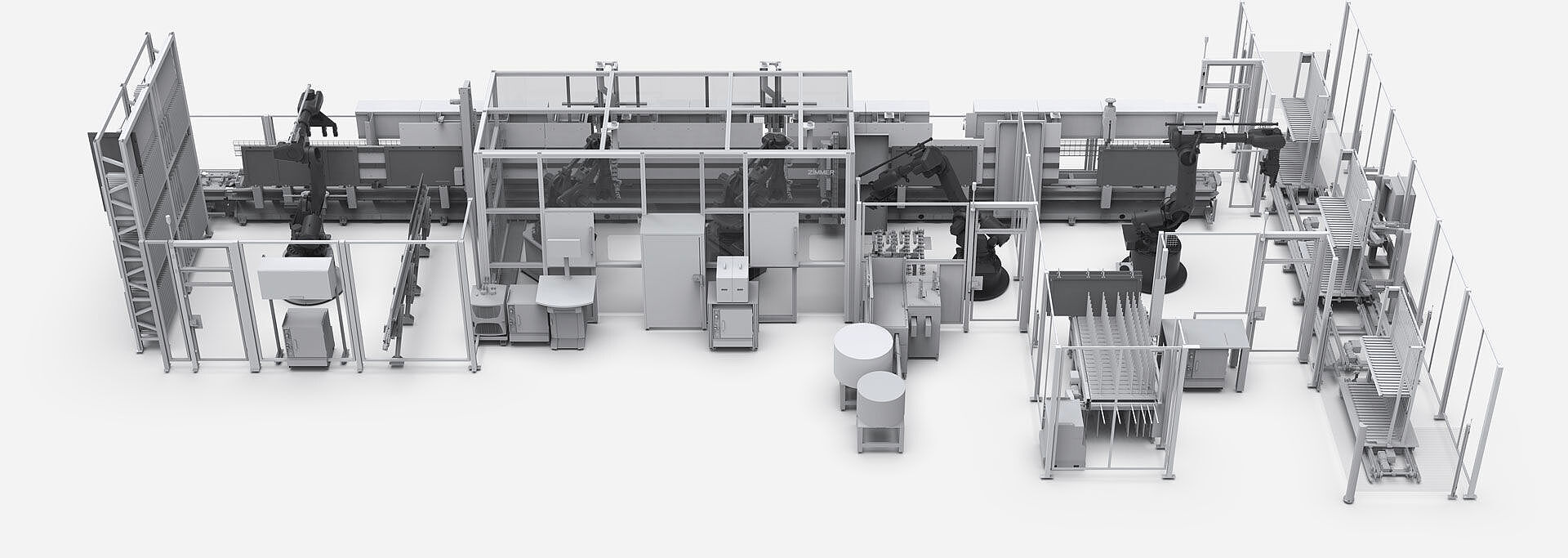
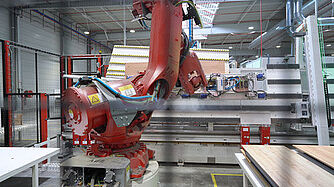
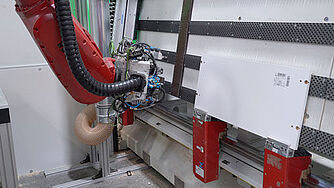
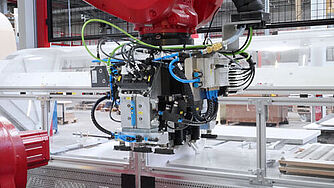
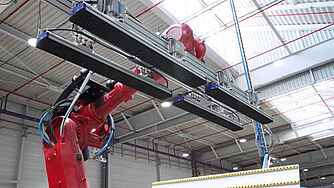
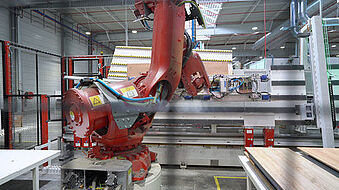
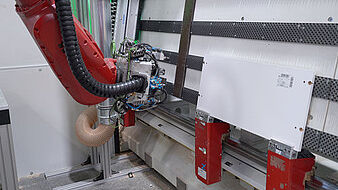

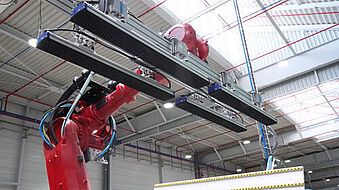
Robot-based sorting
In addition to drilling, Zimmer Systems realizes applications for sorting furniture parts. These cells are integrated into an overall process; alternatively, it can also be used as a stand-alone application.
Sorting concepts with the following parameters:
- System for an output of 2.0 to 25.0 parts per minute
- Storage and retrieval via separate conveyor levels
- Individual robot-based cells that manipulate several parts simultaneously
- Storage volume can be adapted to requirements
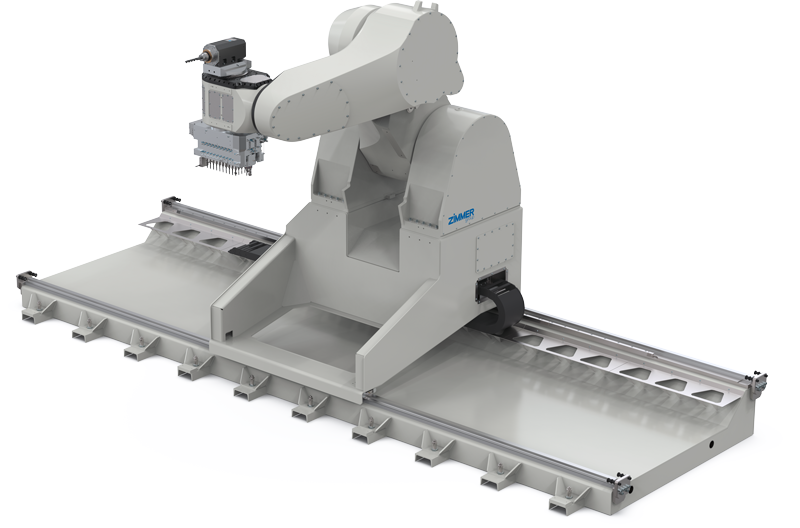
Raptor – processing robot
Our woodworking robot has a number of convincing advantages over conventional machining centers:
- Different tasks with just one machine: Nesting, milling, pre-assembly, part manipulation
- 6-sided machining without manual intervention or separate technical equipment
- Multifunctional head with 2 flanges
- High cutting performance and payload
- Maintenance-friendly and modular design = high availability
- Separation of cutting and handling = short chip-to-chip times
- Spatial removal of dirt-prone components from the machining point
Modular components for machines and lines
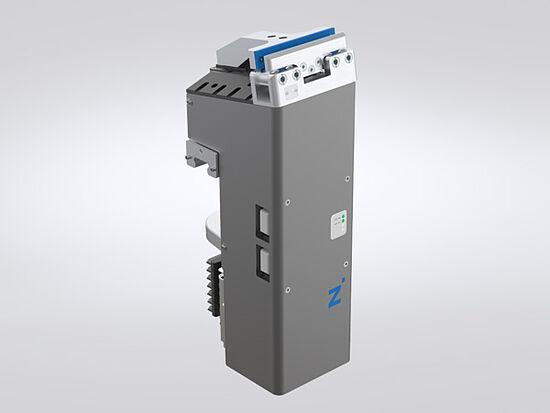
Modular transport system
The Modular Transport System perfectly combines the functions of transportation, processing and quality assurance.
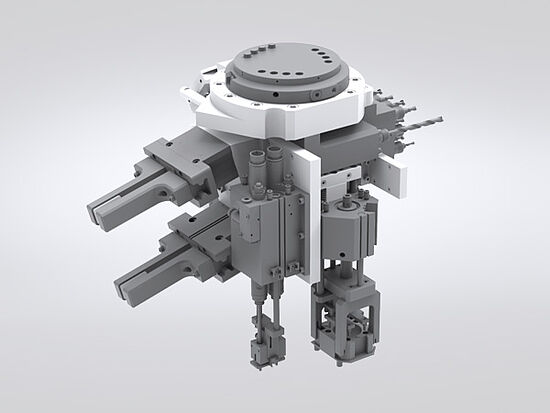
Multifunction unit
The modular, application-optimized multifunctional units from the Zimmer Group give you maximum flexibility for implementing a wide range of functions on the processing module.
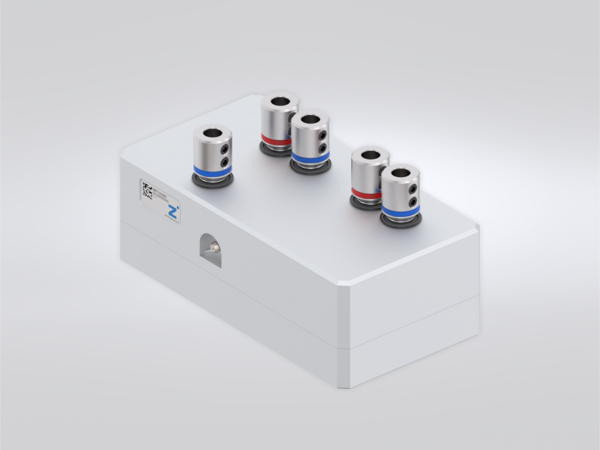
Drilling units with fixed spindles
Customized rigid drilling units in various designs for processing wood, composite materials and plastics.
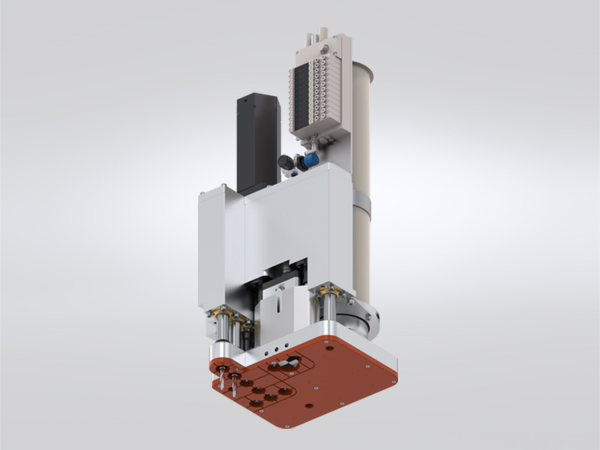
Drilling units with extensible spindles
Customized adjustable drilling gears in a wide range of variations with a variable number of spindles and arrangements for different machining options.
Innovation in woodworking!
The Zimmer Group has been one of the most innovative companies in the woodworking sector for over 25 years. In the 1990s and 2000s, we revolutionized the market with pioneering solutions such as the world’s first e-interface on the processing head, primarily as a think tank and OEM supplier. Today, we deliver sophisticated high-tech in the process chain with a focus on maximum flexibility, scalability and productivity. To this end, we rely on the latest development technologies and simulation methods, such as the digital twin and use these to design and implement complete production and assembly cells that offer maximum flexibility.
The basis for these innovative machine concepts includes a highly flexible, scalable transport module for workpiece transport. Individually and independently controllable transport units (shuttles) make rigid coupling of the transport by a conveyor belt unnecessary. Depending on requirements, an extremely agile and highly dynamic transport circuit with full scalability and any number of shuttles can be set up.
Interaction of components in complex systems
- Decades of experience in the field of woodworking contribute to the intelligent transport system of a drilling and milling center.
- The Zimmer Group’s Modular Transport System is individually adapted to customer and market requirements.
- Guaranteed maximum performance due to scalable minimum gap in the parts flow with batch size 1.
- Use of standardized and reliable grippers with individualized gripper fingers guarantee longevity and system availability.
- State-of-the-art drilling technology with integrated extraction ensures availability and system performance.
- State-of-the-art machining technology with specially developed motor spindles ensures maximum running smoothness and durability, thus guaranteeing the highest possible availability.
- In the woodworking sector, the Zimmer Group works closely with renowned companies such as IMA Schelling Group GmbH.