Clamping and braking elements
Clamping and braking elements are crucial components for positioning, holding and braking. They ensure precision in machining processes, enable efficient production with short cycle times and provide a secure hold for the system or machine. Use our Product Finder to find the right component for your application or get individual advice from our experts.
Are you looking for the right clamping element for your rail and carriage type? Our Product Finder for clamping and braking elements helps you to select the right component and enables you to make an informed decision quickly and easily based on the parameters you enter. Try it out now!
Technology highlight: Zimmer Group clamping and braking elements
ZIMMER GROUP IS A PIONEER IN THE FIELDS OF CLAMPING AND BRAKING ON PROFILE AND ROUND SHAFT GUIDES.
More than 30 years of development and market experience have yielded more than 4,000 products. Zimmer Group offers the most comprehensive and innovative portfolio of products and services reflecting the highest possible quality and reliability. Clamping and braking elements from the Zimmer Group routinely perform critical positioning, holding and braking tasks. They ensure precision during cutting processes and boost efficiency with short cycle times. Their secure hold maximizes safety and protects the user and the machine.
ZIMMER GROUP CLAMPING AND BRAKING ELEMENTS – POWERFUL, DURABLE, INNOVATIVE
With many years of product and market experience, we have a special ability to develop custom solutions that complement our large and diverse range of products.
YOUR BENEFITS:
- Highest holding forces with the smallest design
- No relative movement during the clamping process
- No clamping forces acting on the rail carriage
- High positioning accuracy
- High rigidity
- Virtually wear-free
- Available for all common rail manufacturers
- Series suitable for emergency stop with integrated special surface for braking
FAQ – FREQUENTLY ASKED QUESTIONS ABOUT CLAMPING AND BRAKING ELEMENTS
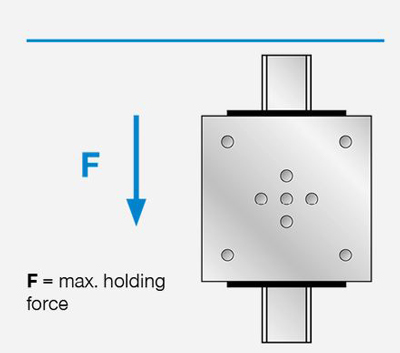
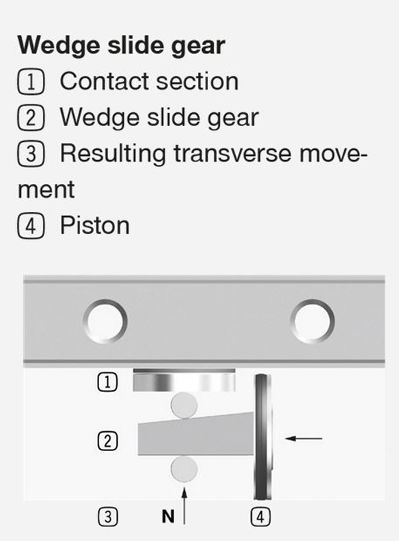
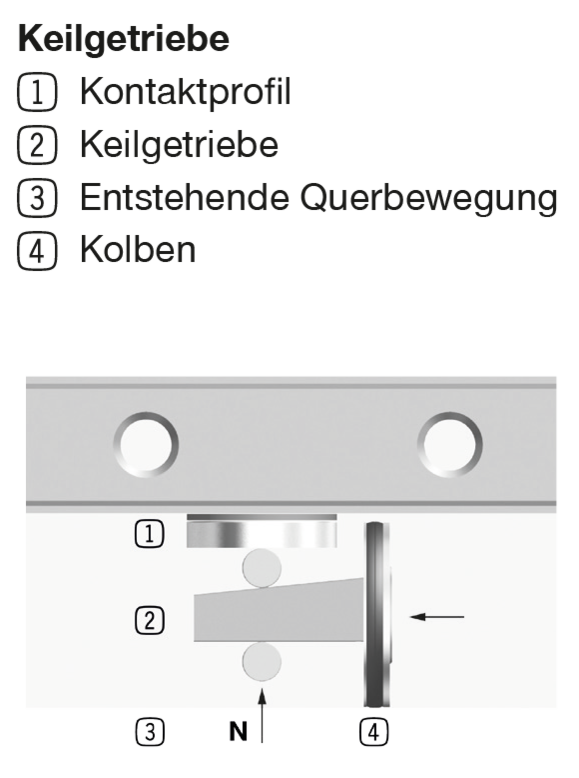
Holding force
The holding force is the maximum force that can be applied in the axial direction. The specified holding forces are tested for each clamping and braking element before delivery with a lightly oiled lubricating layer (ISO VG 68). The use of other oils or lubricants can affect the influence of the friction factor, which can lead to a loss of holding force in individual cases.
Active clamping elements are normally open (NO) and are closed by compressed air, while passive clamping elements (NC) are held closed by the force of a spring energy accumulator when depressurized and must be opened with compressed air. Both variants are characterized by the use of a high-transmission wedge gear. It converts the force of the piston into a transverse holding force via smooth-running rollers and enables very high holding forces without jamming permanently.
Wedge gear
With the wedge gear, the Zimmer clamping and braking elements create the conditions for short cycle times and high machine utilization, while at the same time ensuring reliability in production with a service life of up to 5 million clamping cycles.
General information
- The MBPS/UBPS/LBPS/KBHS/LBHS and RBPS series also allow dynamic use (braking) as a safety feature by using appropriate contact profiles.
- The frictional connection between the clamping element and the linear guideway is always created on the free surfaces of the guide rail, which means that the guide rails of the ball or roller guides are not damaged.
- The clamping elements do not perform any guiding function. It is therefore not possible to replace a carriage with a clamping element. The ideal position of the clamping element is between two carriages.
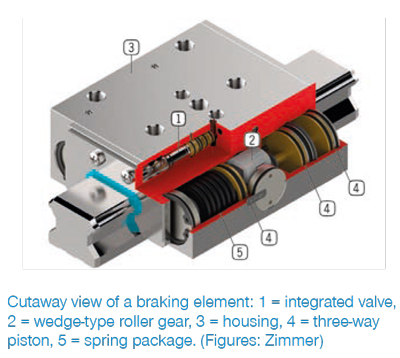
Valve for a quick stop
Braking elements play a key safety role in machining and handling systems, as they ensure that machines and lines come to a standstill as quickly as possible in an emergency. In order to shorten the response time of its braking elements, the Zimmer Group has integrated a globally unique feature into its UBPS series braking elements: The electric valve for triggering the braking or clamping process is not located several meters away, as was previously the case, but directly in the braking element itself.

Shorter closing time – more safety
This has a significant impact on the braking distance. For a vertical axis with an initial speed of 0.5 meters per second, the total braking distance increases considerably compared to the solution with an integrated valve. With a hose length of one meter, the increase is almost 50 percent; with a hose length of 6.5 meters, the braking distance is even almost 250 percent longer.
The Zimmer Group demonstrates its technological expertise with a new product: Following a development phase of over two years, the company is launching a hydraulic braking element that consists of a single functional component, contains no moving parts and uses just the internal stress of the base body to generates braking and holding forces.
The extremely slimline LBHS series essentially consists of a patented “unibody” housing that contains neither pistons nor springs or other moving and therefore wear-prone parts. Oil ducts and recesses are simply machined into the housing block using wire erosion. If hydraulic oil is applied to this basic body, it expands slightly to release the guide rail.
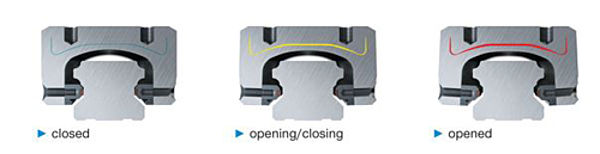
If the hydraulic pressure drops, the element returns to its original shape and presses the two brake shoes against the linear guide. The LBHS is therefore closed when depressurized and thus offers an integrated emergency function that ensures the safe stop of moving components in the event of pressure loss or failure of the entire system.
UBPS series
Cylinder head handling for ship engines
UBPS braking element with high positioning accuracy for specifying the gripper position and ensuring that power is stored when the system is in emergency stop mode due to a power supply failure.
MBPS series
Crankshaft handling with variable gripping distance
MBPS braking elements which hold the grippers securely in position without requiring energy thanks to the built-in spring accumulator.
MKRS series
Box filling system
MKRS clamping element for round guides, which holds the box in place during overhead filling.
MKS series
MKS clamping element, which ensures the position of the gripper fingers and the gripper force without using energy via the built-in spring accumulator.
Zimmer Group gripper with integrated clamping element
GHK gripper with integrated clamping element for force-locking gripping force retention in a compact design.
TPS + MKS series
Rotary clamping element TPS, which fixes the crankshaft housing exactly at the set angle of rotation. In combination with two MKS clamping elements, which secure the gripped crankshaft housing via the built-in spring accumulator.