Wireless functionality for all IO-Link grippers
BCM and MCM
Especially in robotics, the last robot axis, also called the wrist, lacks an appropriate electrical interface for intelligent grippers because this connection is often not available with a suitable cable in the robot arm. This problem is usually solved by routing an external cable along the robot arm. However, this results in some disadvantages, like in the robot’s freedom of movement. Wireless transmission of the required signals and information provides a solution. The combination of BCM [Bridge Communication Module] and MCM [Master Communication Module] offers precisely this functionality. The only thing needed at the actuator is the power supply – an effective solution, not just for robotics.
YOUR BENEFITS
- Compatible with all Zimmer Group IO-Link gripper components, no matter which robot or system base
- No complicated wiring through the robot or the system needed
- No mechanical obstacles or broken wires, thanks to wireless communication
- Scalable, easy expansion with additional grippers due to pairing at the master
Interference-free communication
With the new IO-Link bridge communication modules, the connecting lines between the gripper and the control system can be significantly reduced, while maintaining the same performance and functionality as wired solutions. The features mentioned above allow the new bridge modules to communicate with a wireless IO-Link master securely and without interference. This enables real-time latency times of 5 ms for communication with up to 40 devices for maximum reliability and flexibility in production. The reliability is above a packet error rate (PER) of 10–9.
Two variants BCM-B and BCM-I available
Two versions of the bridge module are currently available. One is the BCM-B, a model that can be positioned decentrally in the wiring harness and enables the connection of an IO-Link actuator. The other is the BCM-I, which allows the use of up to four IO-Link devices. For example, this means that several Zimmer Group grippers and IO-Link-capable sensors can be used at the same time.

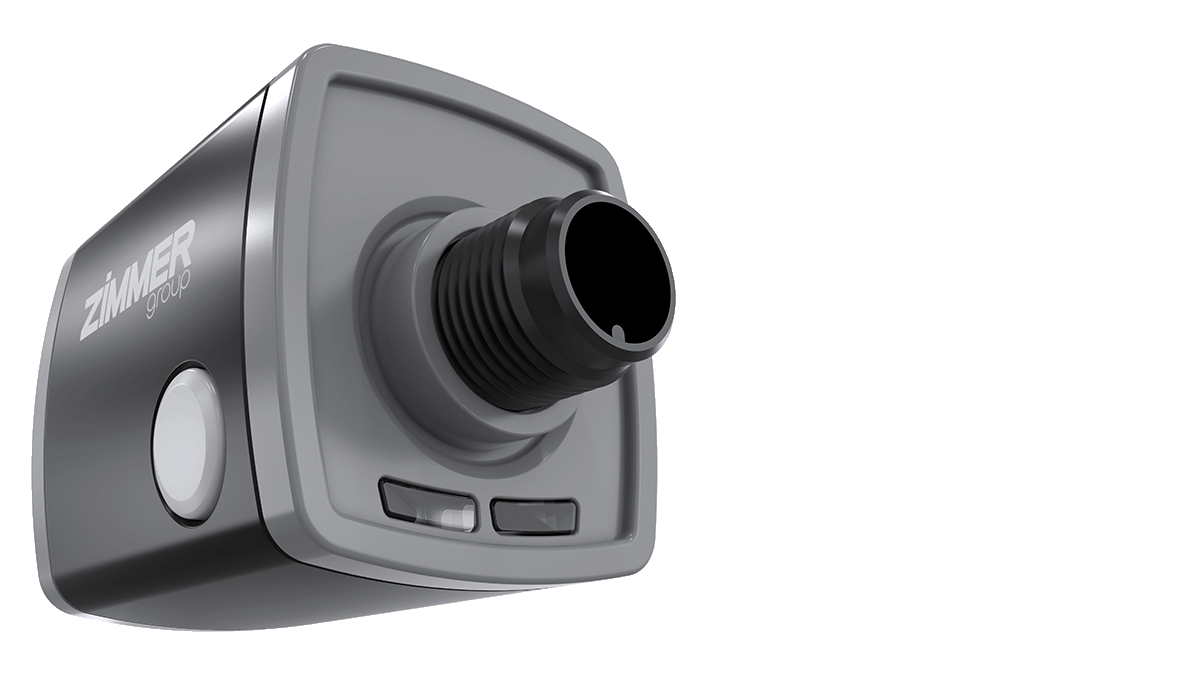
BCM SERIES
Powerful and flexible
The BCM series modules have a current carrying capacity of 4 or 5 amps. This means that no compromises need to be made when selecting the end effectors and even powerful grippers can be controlled via the modules.
MCM series
Reliable data transmission
The counterpart to the BCM. With the Master Communication Module, you receive secure, reliable transmission of data through redundant signals and a maximum packet data error rate of 10⁻⁹.
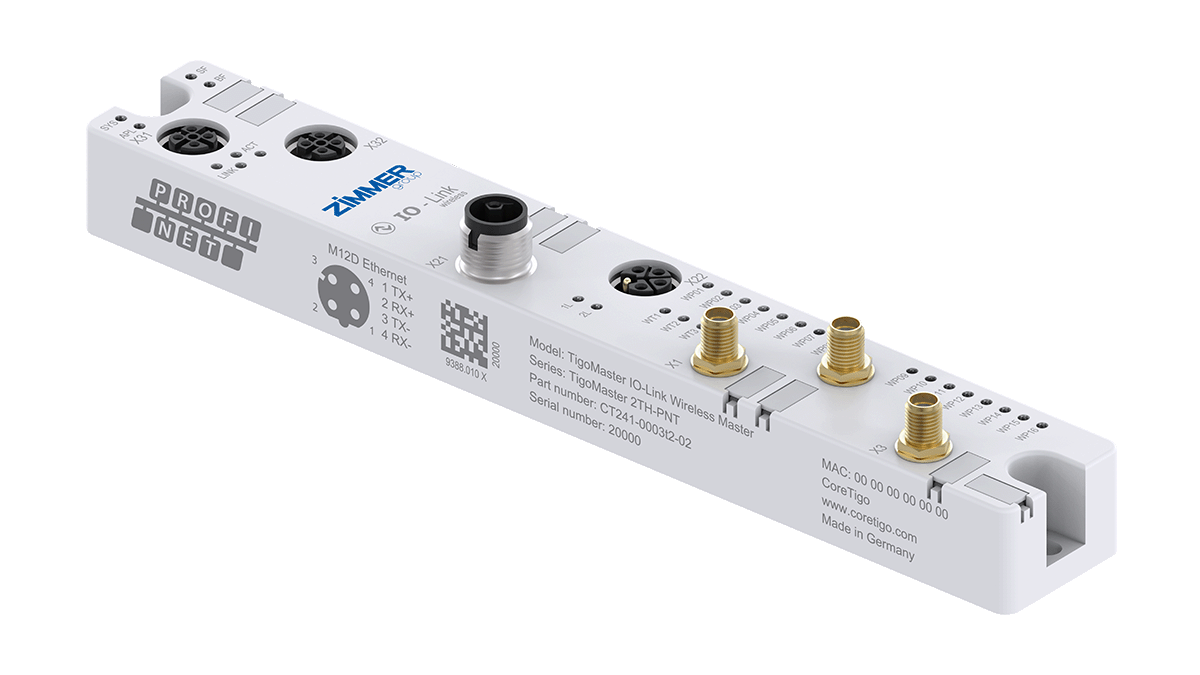
ZIMMER GROUP END EFFECTORS – INTEGRATION WITH IO-LINK WIRELESS TECHNOLOGY
The grippers connected to the bridge modules are controlled by an MCM, which can be integrated in its various versions at fieldbus level. In addition to the specific function blocks for controlling our IO-Link grippers, corresponding instructions are also available. Everything from a single source – so you can reach your goal quickly.
Wirelessly efficient and flexible
BCM and MCM in a single packaging system
ROTZINGER PharmaPack GmbH needed a gripping system for a multi-carrier system for handling individual cookie packs that would meet the requirements of the linear drives. In particular, the cabling in a circulation system is usually a major challenge. The Zimmer Group provided the solution. Click here for the detailed user report: