MAGNETIC GRIPPERS FOR CYLINDRICAL CELLS
CELL PRODUCTION FOR E-MOBILITY
Space-saving and powerful
The gripping of cylindrical cells during the production of electric vehicles presents a particular challenge. The cylindrical cells must be nested in this process, which means they consolidated as closely as possible to enable optimal use of the limited space in the vehicle. This is only possible when the gripper is located in the shadow of the battery.
With the HPM2000 series, this process-relevant design was implemented and combined with a holding force of 65 N, which ensures that cylindrical cells will be held securely even at the highest accelerations and during an emergency stop. The low residual holding force under 1 N when the magnets are deactivated not only enables reliable depositing. It also fulfills the requirements for technical cleanliness.
The focus is on modular thinking to enable the gripper to be optimally adapted to the respective process. The gripper can be combined with both a piston position sensor and a battery presence sensor. In addition, axis compensators available that work together with centering plates to compensate for misalignment of cells that occurs in the various manufacturing processes.
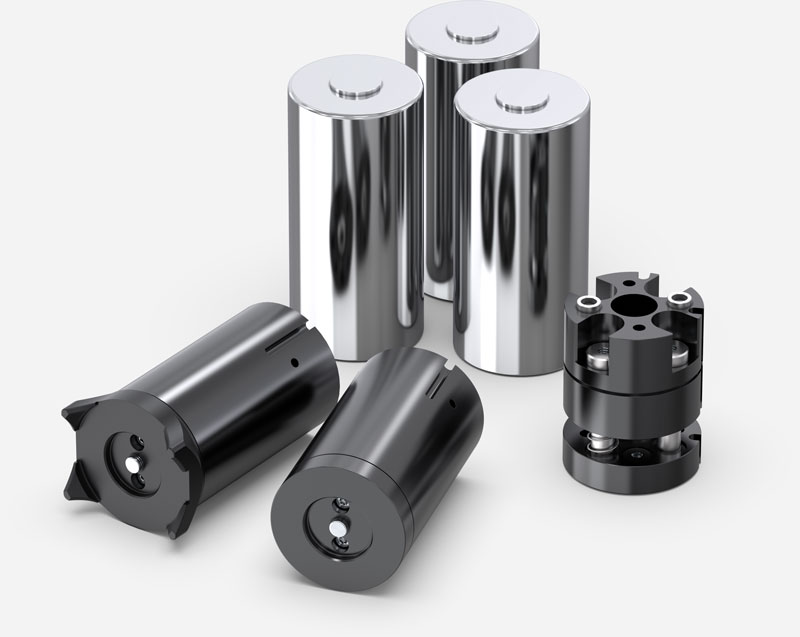
SINGLE OR DOUBLE-ACTING
VERSION AVAILABLE
SAFE SENSING DUE TO CENTERED
INDUCTIVE SENSOR
OPTIMIZED FOR THE CENTER DISTANCE
THE 46-MM CYLINDRICAL CELL
FEATURES IN DETAIL
SENSORS
In addition to the magnet position, the integrated sensor also reliably checks whether a cell is present. The positive terminal of the cell is inductively scanned by a spring-loaded plunger. In addition, the sensing is centered, which means that a cell that is not correctly placed on the contact surface is detected 100%. This is a huge advantage over sensing from the side, because it increases the accuracy and reliability of detection.
CONTACT SURFACE
The HPM2000 series offers two cover variants: flat [1] and with four centering aids [2]. The cover is decoupled electrically to prevent uncontrolled unloading of the cell above the gripper. In the event of damage, the cover can be changed easily without the entire gripper needing to be replaced. Pre-centering ensures holding with positioning accuracy. To increase the packing density of the battery, the geometry was designed so that the center distance is <47.5 mm.
Z-COMPENSATION
The Z-compensation, available as an accessory, is used for collision prevention and prevents crashes. It also compensates for height differences in the cells. This ensures that the cell can be positioned securely on the contact surface. For gentle and reliable handling!
DRIVE
You can choose between two drive variants depending on the application and the requirements. The single-acting variant with spring return [1] has just one hose line and therefore requires less compressed air. The double-acting drive [2], in contrast, delivers incredibly fast cycle times.